50 interview questions and answers on air compressors
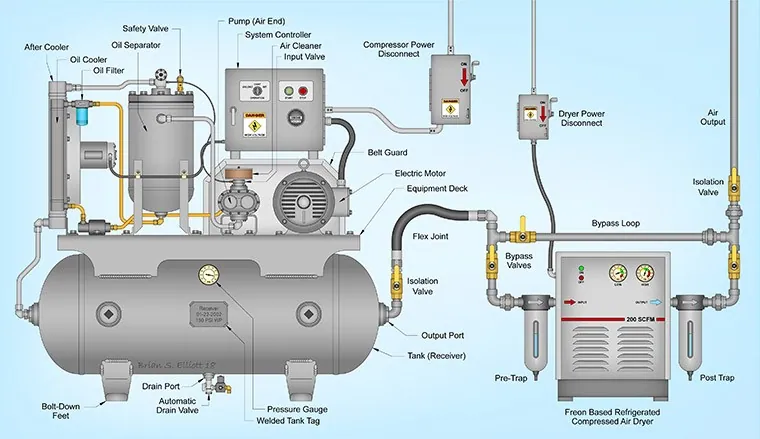
What is an air compressor?
An air compressor is a device that converts power (usually from an electric motor, diesel engine, or gasoline engine) into potential energy stored in pressurized air.
What are the types of air compressors?
There are several types, including reciprocating, rotary screw, rotary vane, centrifugal, and axial compressors.
What factors determine the choice of an air compressor?
Factors include required pressure, volume of air needed, power source available, operating conditions, and budget.
How does a reciprocating air compressor work?
Reciprocating compressors use a piston in a cylinder to compress air. The piston moves up and down, drawing air into the cylinder on the downstroke and compressing it on the upstroke.
What are the advantages of reciprocating compressors?
They are relatively inexpensive, have a simple design, and are suitable for intermittent use.
What are the disadvantages of reciprocating compressors?
They tend to be noisy, have higher maintenance requirements, and are less efficient compared to other types.
How does a rotary screw compressor work?
Rotary screw compressors use two interlocking helical screws to compress air. As the screws rotate, air is drawn in and compressed between them.
What are the advantages of rotary screw compressors?
They are efficient, operate quietly, and are suitable for continuous duty.
What are the disadvantages of rotary screw compressors?
They are more expensive upfront and may require specialized maintenance.
What is the difference between oil-lubricated and oil-free compressors?
Oil-lubricated compressors use oil for lubrication and cooling, while oil-free compressors use alternative methods to reduce friction and heat.
What are the applications of air compressors?
Applications include powering pneumatic tools, inflating tires, operating HVAC systems, and supplying air for industrial processes.
How do you calculate the air compressor’s horsepower requirement?
Horsepower requirement depends on the desired flow rate and pressure. It can be calculated using the formula: Horsepower = (Flow rate × Pressure) / (Overall efficiency × 550).
What is CFM in air compressors?
CFM stands for Cubic Feet per Minute and represents the volume of air that the compressor can deliver at a given pressure level.
How do you determine the right size of an air compressor for a specific application?
You need to consider the required CFM, operating pressure, duty cycle, and any additional factors specific to the application.
What is the duty cycle of an air compressor?
The duty cycle refers to the percentage of time that the compressor can operate continuously without overheating or experiencing mechanical issues.
What safety precautions should be taken when working with air compressors?
Safety precautions include wearing appropriate protective gear, ensuring proper ventilation, following manufacturer’s guidelines, and regularly inspecting equipment for damage or leaks.
How do you maintain an air compressor?
Maintenance tasks may include checking oil levels, inspecting filters, cleaning components, tightening connections, and scheduling regular service intervals.
What are the common causes of air compressor failures?
Common causes include overheating, worn-out components, inadequate lubrication, electrical issues, and air leaks.
How do you troubleshoot air compressor problems?
Troubleshooting involves identifying symptoms, checking for obvious issues such as leaks or loose connections, and systematically inspecting components to isolate the problem.
What are the signs of air compressor wear and tear?
Signs include increased noise, reduced performance, oil leaks, excessive vibration, and irregular pressure output.
How do you prevent moisture buildup in an air compressor system?
Using a moisture separator, draining condensate regularly, ensuring proper ventilation, and installing dryers can help prevent moisture buildup.
What is the purpose of an air receiver tank in an air compressor system?
An air receiver tank stores compressed air, stabilizes pressure fluctuations, and allows for smoother operation by reducing the number of starts and stops.
What is the role of a pressure relief valve in an air compressor?
A pressure relief valve prevents the system from exceeding the maximum pressure by releasing excess air when the pressure reaches a preset limit.
How do you size an air receiver tank?
Sizing depends on factors such as compressor capacity, duty cycle, pressure requirements, and desired pressure stability. Generally, a larger tank can provide more storage capacity and better pressure control.
How do you prevent air compressor overheating?
Ensuring proper ventilation, maintaining adequate lubrication, monitoring operating temperatures, and avoiding overloading the compressor can help prevent overheating.
What is the role of air filters in an air compressor?
Air filters remove contaminants such as dust, oil, and moisture from the intake air, preventing damage to internal components and ensuring clean compressed air output.
How do you select the right type of air filter for an air compressor?
Consider factors such as filtration efficiency, airflow capacity, compatibility with the compressor system, and maintenance requirements when selecting air filters.
What is the function of an air/oil separator in a rotary screw compressor?
An air/oil separator separates compressed air from lubricating oil, ensuring clean, oil-free air output and preventing oil contamination in the compressed air system.
What are the advantages of using compressed air as a power source?
Advantages include portability, versatility, ease of use, and the ability to generate high power levels without the need for complex mechanical systems.
How do you calculate the efficiency of an air compressor?
Efficiency is calculated by dividing the compressor’s actual power consumption by its theoretical power requirement and multiplying by 100 to get a percentage.
What is the difference between single-stage and two-stage air compressors?
Single-stage compressors compress air in one step, while two-stage compressors compress air in two successive stages, resulting in higher pressure levels.
What factors affect the efficiency of an air compressor?
Factors include design, operating conditions, temperature, humidity, altitude, and maintenance practices.
How do you control the pressure output of an air compressor?
Pressure can be controlled using a pressure switch, which activates the compressor motor to maintain a preset pressure level within the system.
What is the role of a check valve in an air compressor system?
A check valve prevents compressed air from flowing back into the compressor when it shuts off, helping to maintain pressure in the system and preventing damage to the compressor.
How do you calculate the required compressor displacement for a specific application?
Compressor displacement is calculated by dividing the required CFM by the compressor’s volumetric efficiency and multiplying by 1,440 (the number of minutes in an hour).
What are the advantages of using pneumatic tools powered by air compressors?
Advantages include lightweight, compact design, high power-to-weight ratio, and the ability to operate in hazardous environments.
How do you ensure proper air quality in a compressed air system?
Proper air quality can be ensured by using appropriate filtration, drying equipment, regular maintenance, and monitoring for contaminants such as oil, moisture, and particulates.
What is the role of a compressor regulator in an air compressor system?
A compressor regulator controls the pressure output by adjusting the airflow to the pneumatic tools or equipment connected to the system.
How do you prevent air compressor oil contamination?
Preventing oil contamination involves using high-quality lubricants, ensuring proper filtration and separation, monitoring oil levels, and conducting regular maintenance checks.
What are the environmental considerations when operating air compressors?
Environmental considerations include noise pollution, emissions, energy consumption, proper disposal of lubricants and contaminants, and compliance with regulations.
How do you diagnose and repair air compressor leaks?
Diagnosis involves inspecting connections, fittings, hoses, and components for signs of leaks and using methods such as soapy water or pressure testing to identify the source. Repairs may involve tightening connections, replacing seals, or repairing damaged components.
What safety measures should be taken when performing maintenance on air compressors?
Safety measures include disconnecting power sources, relieving pressure from the system, wearing appropriate protective gear, and following lockout/tagout procedures to prevent accidental startup.
How do you optimize energy efficiency in an air compressor system?
Optimizing energy efficiency involves selecting the right size and type of compressor, minimizing air leaks, maintaining proper operating conditions, using energy-efficient components, and implementing control strategies such as load/unload or variable speed drive.
What are the key components of an air compressor system?
Key components include the compressor unit, motor or engine, air intake system, filtration system, lubrication system, cooling system, control panel, air receiver tank, and distribution network.
How do you calculate the total cost of ownership for an air compressor?
Total cost of ownership includes initial purchase cost, installation expenses, maintenance costs, energy consumption, repair and replacement costs, and disposal/recycling costs over the equipment’s lifespan.
What are the safety hazards associated with operating air compressors?
Safety hazards include high pressure, electrical hazards, noise exposure, vibration, heat generation, and potential for accidents such as leaks, ruptures, or explosions.
How do you prevent air compressor oil contamination?
Preventing oil contamination involves using high-quality lubricants, ensuring proper filtration and separation, monitoring oil levels, and conducting regular maintenance checks.
What are the environmental considerations when operating air compressors?
Environmental considerations include noise pollution, emissions, energy consumption, proper disposal of lubricants and contaminants, and compliance with regulations.
How do you diagnose and repair air compressor leaks?
Diagnosis involves inspecting connections, fittings, hoses, and components for signs of leaks and using methods such as soapy water or pressure testing to identify the source. Repairs may involve tightening connections, replacing seals, or repairing damaged components.
What safety measures should be taken when performing maintenance on air compressors?
Safety measures include disconnecting power sources, relieving pressure from the system, wearing appropriate protective gear, and following lockout/tagout procedures to prevent accidental startup.
You may also like