Interview questions and answers on preventive maintenances and execution
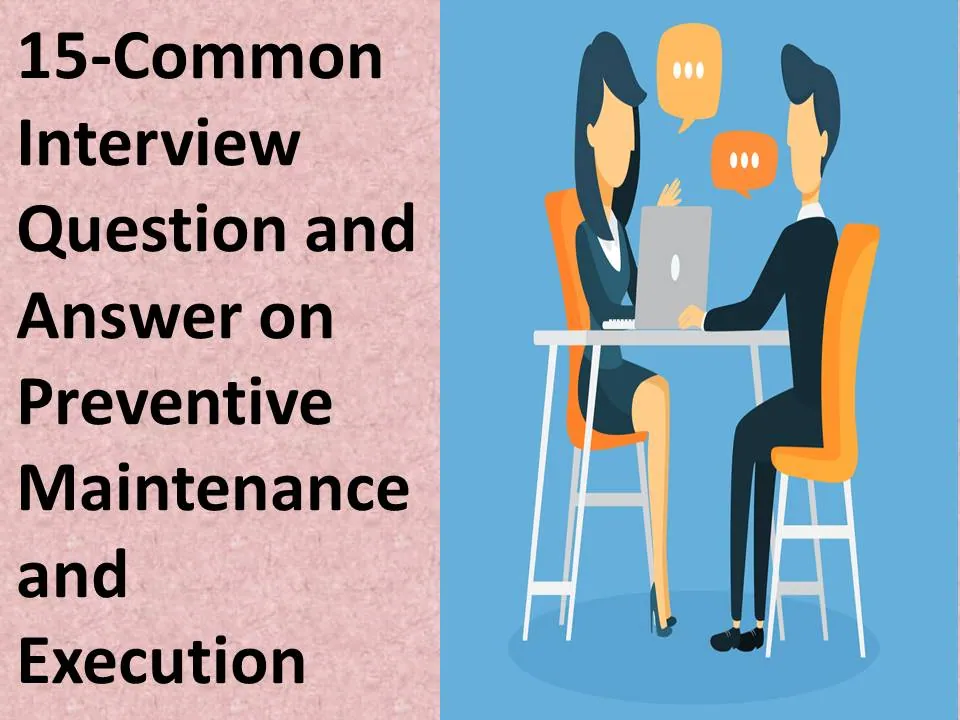
What is preventive maintenance, and why is it important?
Preventive maintenance involves regular inspections, repairs, and upkeep of equipment to prevent breakdowns and prolong its lifespan. It’s important because it reduces downtime, improves safety, and saves costs in the long run.
What strategies would you employ to implement an effective preventive maintenance program?
I would start by conducting a thorough assessment of all equipment, create a schedule for regular inspections and maintenance tasks, prioritize critical equipment, train staff on maintenance procedures, and utilize technology such as CMMS (Computerized Maintenance Management System) for tracking and scheduling.
How do you prioritize maintenance tasks in a preventive maintenance program?
I prioritize tasks based on criticality, safety concerns, historical data on equipment failures, manufacturer recommendations, and regulatory requirements.
Can you discuss a successful preventive maintenances project you’ve led in the past?
Discuss a specific project where you effectively implemented a preventive maintenance program, including the steps you took, challenges faced, and the results achieved.
How do you ensure compliance with preventive maintenance procedures?
I ensure compliance by regularly auditing maintenance activities, providing proper training to staff, implementing standardized procedures, and utilizing digital tools for tracking and documentation.
What role does data analysis play in preventive maintenances?
Data analysis helps identify patterns of equipment failures, optimize maintenance schedules, predict potential issues before they occur, and improve overall equipment reliability.
How do you handle unexpected breakdowns despite a preventive maintenances program?
I address unexpected breakdowns by having contingency plans in place, prioritizing repairs based on criticality, investigating the root cause of the failure, and adjusting the preventive maintenance program accordingly.
How do you ensure that preventive maintenance tasks do not disrupt production schedules?
I plan preventive maintenance during scheduled downtimes, coordinate with production teams to minimize disruptions, and prioritize tasks to minimize impact on production schedules.
What steps do you take to ensure the safety of maintenance personnel during preventive maintenance activities?
I ensure safety by providing proper training, enforcing the use of personal protective equipment (PPE), conducting risk assessments, implementing lockout/tagout procedures, and maintaining clear communication protocols.
How do you measure the effectiveness of a preventive maintenances program?
I measure effectiveness by tracking key performance indicators (KPIs) such as equipment uptime, mean time between failures (MTBF), maintenance costs, and comparing them against established benchmarks or industry standards.
How do you handle resistance from stakeholders towards implementing preventive maintenances?
I address resistance by clearly communicating the benefits of preventive maintenance, providing data-driven evidence of its effectiveness, involving stakeholders in the decision-making process, and addressing their concerns proactively.
Can you discuss a time when you had to troubleshoot a complex maintenance issue during preventive maintenances?
Describe a specific scenario where you successfully troubleshooted a complex maintenance issue during preventive maintenance, including the steps you took and the outcome.
How do you stay updated on new technologies and best practices in preventive maintenances?
I stay updated by attending industry conferences, participating in professional development programs, networking with peers, and subscribing to relevant publications and online forums.
How do you ensure that spare parts inventory is managed effectively to support preventive maintenances activities?
I ensure effective spare parts management by conducting regular inventory audits, maintaining adequate stock levels based on usage patterns and lead times, implementing a system for tracking and reordering parts, and prioritizing critical components.
How do you foster a culture of continuous improvement within the maintenance team?
I foster a culture of continuous improvement by encouraging open communication, soliciting feedback from team members, recognizing and rewarding innovative ideas, and providing opportunities for training and skill developmen.
You may also like