Table of Contents
Gerotor Pump
A gerotor pump is a type of positive displacement pump that utilizes an eccentrically mounted rotor inside a stator to generate fluid flow. It is commonly used in various applications, including hydraulic systems, automotive engines, and oil pumps. The name “gerotor” is a combination of “generated” and “rotor,” highlighting the way in which fluid is generated by the rotating components.
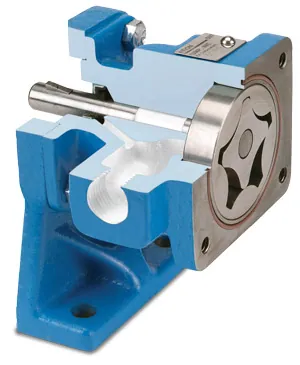
Working Principle of Gerotor Pump
Gerotor pump work on the principle of internal gear pump by using gear shaped rotor elements meshing internally.
A gerotor pump is a type of positive displacement pump that uses the interaction of rotating gears to pump fluid. It consists of an outer gear (rotor) and an inner gear (idler) that mesh together to create chambers. As the gears rotate, the fluid is trapped in the chambers and carried from the suction side to the discharge side of the pump.
Inlet Phase: As the inner rotor turns, fluid is drawn into the pump through the inlet port. The expanding cavity between the inner and outer rotors creates a low-pressure zone, causing fluid to flow into this space.
Compression Phase: As the rotors continue to rotate, the cavity between the rotors decreases in size, compressing the fluid. This compression increases the pressure of the fluid.
Outlet Phase: The compressed fluid is forced out of the pump through the outlet port as the cavity between the rotors opens up. This creates a continuous flow of fluid.
Construction of Gerotor Pump
Gerotor pump is a positive displacement pump. The name gerotor is derived from “generated rotor”. A gerotor unit have an inner and outer rotor. The inner rotor has n teeth, while the outer rotor has n+1 teeth.The axis of the inner rotor is offset from the axis of the outer rotor. These both rotors rotate on their respective axes.
It consists of following parts :
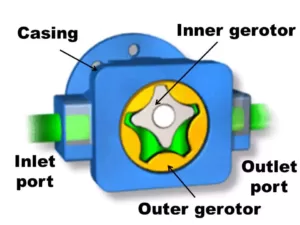
1) Outer ring : The outer ring is a casing in which gerotor pair is mounted.
2) Outer gerotor : Outer gerotor is idler and it has always one tooth more than inner gerotor.
3) Inner gerotor : The inner gerotor is the driver. The number of teeth of the outer and inner gerotor vary. The axis of inner gerotor is offset from the axis of the outer gerotor.
4) Housing: The pump housing encloses the rotors and provides a sealed chamber for fluid displacement. It has inlet and outlet ports for fluid entry and exit.
5) Suction and discharge port : The suction and discharge ports are provided to suck and deliver oil respectively.
Working of Gerotor Pump
When inner gerotor rotates with the help of motor, it creates partial vaccum near the suction portwhen mesh with the outer gerotor. The oil enters through the suction port.
If the number of teeth for the inner and outer gerotor are four and five respectively, then while the inner gerotor makes one revolution, the outer one makes only 4/5 revolution.
Due to offset movement between inner and outer gerotor, the volume near the delivery port decreases and oil is forced out through delivery port.
The care should be taken as gerotor are to be manufactured with high precision otherwise internal leakage becomes excessive.
It can operate at the pressure of 125bar, maximum speed of 2000-3600 rpm with maximum discharge of 200 lit/min.
Here’s a step-by-step explanation of the working of a gerotor pump:
Initial Position:
The gerotor pump consists of an inner rotor and an outer rotor.
The inner rotor is connected to the drive shaft and typically has one less tooth than the outer rotor.
The outer rotor surrounds the inner rotor and is usually fixed in place within the pump housing.
The pump housing encloses the rotors and has inlet and outlet ports for fluid entry and exit.
Inlet Phase:
As the drive shaft rotates, it causes the inner rotor to spin.
The rotation of the inner rotor creates a cavity between the lobes of the inner and outer rotors.
The pump inlet is positioned at a point where the cavity is expanding, creating a low-pressure zone.
Fluid is drawn into this low-pressure zone through the inlet port.
Compression Phase:
As the inner rotor continues to rotate, the cavity between the rotors decreases in size.
This reduction in cavity volume causes the fluid to be compressed.
The compression of the fluid increases its pressure.
Outlet Phase:
As the cavity between the rotors reaches its smallest volume, the fluid is forced out of the pump.
The pump outlet is positioned at the point where the cavity is contracting, creating a high-pressure zone.
The compressed fluid is expelled through the outlet port.
Continuous Operation:
The rotation of the inner rotor continues, and the cycle repeats.
The continuous rotation of the rotors generates a constant flow of fluid from the inlet to the outlet.
Key Points:
Gerotor pumps operate on the principle of positive displacement, meaning they move a fixed amount of fluid with each rotation.
The number of teeth on the inner and outer rotors determines the pump’s displacement per revolution.
The efficiency of gerotor pumps is influenced by factors such as clearances between the rotors and the pump housing.
Material used for Gerotor Pump
The materials used for constructing gerotor pumps depend on the specific application, the type of fluids being pumped, and the environmental conditions.
Here are some common materials used in the construction of gerotor pumps:
Rotor Materials:
Inner Rotor: Often made of materials like steel or stainless steel. These materials provide strength and durability.
Outer Rotor (Ring Gear): Similar to the inner rotor, the outer rotor is typically made of steel or stainless steel. The choice of material depends on factors like wear resistance and corrosion resistance.
Housing Materials:
Pump Housing: Common materials for the pump housing include aluminum, cast iron, or stainless steel. Aluminum is often chosen for its lightweight properties, while cast iron provides durability. Stainless steel is preferred for its corrosion resistance.
Seals:
Seals are crucial to prevent fluid leakage and maintain the efficiency of the pump. Common seal materials include nitrile rubber, Viton, or other elastomers, depending on the type of fluid being pumped and the temperature conditions.
Bearings:
Bearings are used to support the rotating components of the pump. Materials for bearings can include stainless steel, bronze, or other alloys, depending on the application requirements.
Shaft:
The shaft connects the inner rotor to the drive source. Materials for the shaft may include hardened steel or stainless steel, providing strength and resistance to wear.
Coating or Surface Treatments:
Some components may undergo coatings or surface treatments to enhance their properties. For example, parts may be coated with chrome or other materials to improve wear resistance.
Gaskets and O-rings:
These are used to create a seal between different components. Materials for gaskets and O-rings include rubber or synthetic elastomers compatible with the fluid being pumped.
Bearing Lubrication:
Bearings may require lubrication, and the choice of lubricant depends on the operating conditions. Common lubricants include oils or greases suitable for the specific application.
Application of Gerotor Pump
Gerotor pumps find applications in various industries due to their positive displacement design, compact size, and reliability.
Some common applications of gerotor pumps include:
Hydraulic Systems:
Gerotor pumps are commonly used in hydraulic systems to provide the necessary fluid power for equipment such as hydraulic motors and actuators.
They are suitable for applications where a compact pump design is essential.
Automotive Industry:
Gerotor pumps are employed in automotive systems for tasks such as engine lubrication, transmission fluid circulation, and fuel delivery.
They are often used in engine oil pumps, automatic transmission pumps, and fuel transfer pumps.
Lubrication Systems:
Gerotor pumps are utilized in various industrial machinery and equipment to circulate lubricating oil or grease, ensuring proper lubrication of moving parts.
They are commonly found in applications such as machine tools and industrial gearboxes.
Fuel Systems:
Gerotor pumps are used in fuel systems to deliver fuel from the tank to the engine.
They are often employed in both automotive and industrial applications, providing a reliable means of fuel transfer.
Agricultural Equipment:
Gerotor pumps are used in agricultural machinery for tasks such as transferring fluids, providing hydraulic power for implements, and circulating fluids for cooling systems.
Chemical and Process Industries:
In industries where precise fluid transfer and metering are essential, gerotor pumps can be used for dosing and transferring chemicals.
Their positive displacement characteristics make them suitable for applications requiring accurate flow rates.
Aerospace:
Gerotor pumps are employed in various aerospace applications where compact, lightweight, and reliable pumps are required.
They may be used in hydraulic systems for aircraft landing gear, flaps, and other control systems.
Industrial Machinery:
Gerotor pumps are used in a variety of industrial machinery, including manufacturing equipment, where precise fluid control and power transmission are necessary.
Advantages and Disadvantages
Advantages
Compact Size: Gerotor pumps are known for their compact size, making them suitable for applications where space is limited. Their small footprint allows for easy integration into various systems.
High Efficiency: Gerotor pumps are highly efficient due to the tight clearances between the gears. This design minimizes internal leakage, resulting in improved volumetric efficiency and reduced energy consumption.
Self-Priming Capability: Gerotor pumps have excellent self-priming capabilities, meaning they can draw fluid into the pump without the need for external priming. This feature is beneficial for starting the pump and ensuring continuous operation.
Versatile Fluid Compatibility: Gerotor pumps can handle a wide range of fluids, including liquids with low to moderate viscosities. They are commonly used for pumping oils, fuels, lubricants, hydraulic fluids, and other industrial fluids.
Smooth Flow and Low Pulsation: Gerotor pumps provide a steady and uniform flow of fluid, minimizing pulsations and pressure variations. This makes them suitable for applications that require precise flow control and consistent fluid delivery.
Relatively Low Noise and Vibration: Gerotor pumps operate at relatively low noise and vibration levels due to the meshing action of the gears and the close tolerances maintained between them. This characteristic is beneficial in noise-sensitive environments.
Disadvatages
Limited Operating Speed Range: Gerotor pumps typically have a limited range of operating speeds. High rotational speeds can generate heat, increase wear, and reduce the pump’s overall efficiency and lifespan.
Sensitivity to Contaminants: Gerotor pumps can be sensitive to particulate contaminants present in the fluid being pumped. Abrasive particles can cause wear on the gear surfaces, leading to reduced performance and potential damage.
Limited Pressure Capability: Gerotor pumps may have limitations in terms of the maximum pressure they can handle. Operating at excessively high pressures can cause increased leakage and potential failure.
Maintenance and Service Requirements: Gerotor pumps require proper maintenance, including regular inspection and lubrication. The tight clearances between gears make it important to ensure clean and adequate lubrication to minimize wear and maintain optimal performance.
Cost: Depending on the design and quality, gerotor pumps can be relatively more expensive compared to other types of pumps. The complex gear profiles and tight tolerances involved in their manufacturing contribute to their higher cost.
FAQ
What is the principle of gerotor pump?
It work on the principle of internal gear pump by using gear shaped rotor elements meshing internally.
What is the advantages of gerotor pump?
Constant and even discharge. Operates well in either direction. It has quiet operation.
What type of pump is Gerotor pump?
Gerotor pump is a positive displacement pump.
What is the pressure of gerotor pump?
It can operate at the pressure of 125bar, maximum speed of 2000-3600 rpm with maximum discharge of 200 lit/min.
Are gerotor pumps self priming?
It’s depend on pump manufacturer. Some gerotor pump like SKF product series 143 are self-priming, positive-displacement pumps with fixed displacement and high efficiency.
You may also like