Table of Contents
Starter Motor

A starter motor is an essential component in the ignition system of an internal combustion engine. Its primary function is to crank the engine, enabling it to start.
When you turn the ignition key, an electrical current is sent to the starter motor, which then engages with the engine’s flywheel or flexplate and turns it to initiate the engine’s rotation.
The starting system consist of starting motor, battery, control switch and interconnecting wiring. The preference of all these components must be match against engine requirement for satisfactory service.
The starting motor are mostly of direct current series motor.
This convert the electric energy supplied by the battery to mechanical energy by rotating the armature shaft. A drive mechanism couples the shaft through a pinion and Flywheel ring gear to the engine.
Starter motor or Cracking motor
The Starter Motor is specially designed to produce high turning effort, called starting torque at high speed for a short period.
It has driving mechanism to connect the motor shaft pinion to the engine running gear while cranking and to disconnect is when the engine starts working.
Starting motors are direct current motors operates on large currents at low voltages. The armateur and fields are built with thick wire to keep the resistance low and to enable them to carry large currents without overheating.
At faster turn, less currents without overheating. At faster turn, less current and slower turn more torque they develop.
Construction of Starter Motor
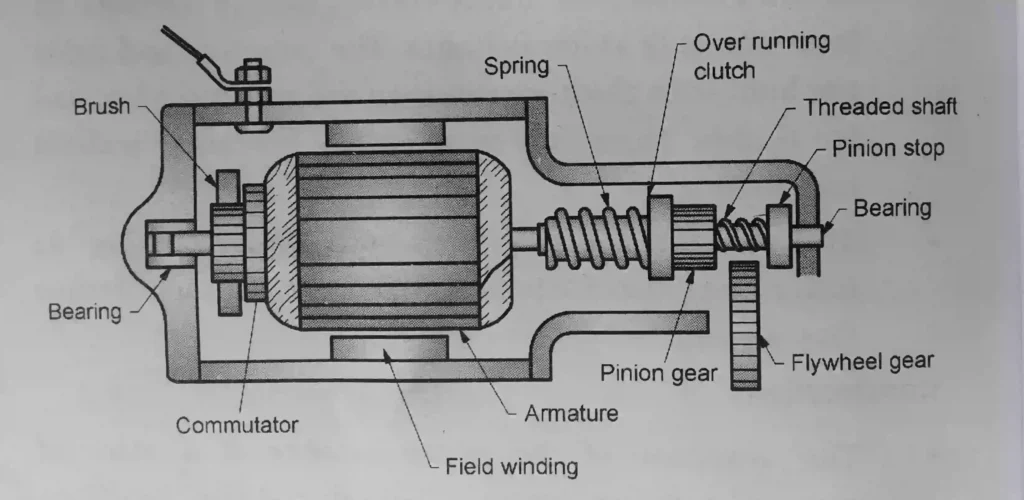
The armature of the motor consists of a stock of stamped soft iron pieces called laminations. Fittef on the armature shaft. Insulated wire is wound through the matching slots in the iron laminations i.e. to provide four electrical paths when four field poles are used.
Each complete winding loops form a commulator segment is completed at an adjustment commulator segment. This should be done all around the armature so that all the windings are interconnected.
The ends of two endings are soldered or welded to junction on each commulator segment bar. The commulator base are from the rest of the armature assembly. These are brushes supported by brush holders. They are held against the commulator by the brush spring.
The brushes are usually anglet slightly to provide good contact minimum arcing and long service life.
Two opposite brushes are insulated from the frame and other brushes are ground to the frame.
One end of the armature shaft is much longer than other end to accommodate the drive assembly. This is opposite to the commulator end.
Starter motor components and their functions
Armature
The armature is an electromagnet, mounted on the drive shaft and support bearings. It is a laminated soft iron core that is wrapped with numerous loops or coils of conductors.
Commutator
The commutator is a section of the shaft at the rear of the housing that the brushes ride on to conduct electricity. The commutator is made up of two plates attached to the armature shaft. These plates provide the two connections for the electromagnet coil.
Brushes
The brushes run over a commutator section at the rear of the housing, making contact with the commutator contacts and conducting electricity.
Solenoid
The solenoid contains two coils of wire that are wrapped around a moving core. The solenoid acts as a switch to close the electrical connection and connects the starter motor to the vehicle’s battery.
Plunger
The plunger works by using the connected vehicle battery and solenoid to push the plunger forward, which engages the pinion gear.
Lever fork
The lever fork is connected to the plunger, so when the plunger is pushed forward, so is the lever fork. This process then activates the pinion.
Pinion
The pinion is a unique combination of gear and springs. Once the starter engages, the gear extends into the gearbox housing and meshes with the flywheel. This spins the engine to start the combustion process.
field coils
The casing holds the boot camps in the casing with screws. It can consist of two to four field coils connected in series. Powered by the battery, it converts the coils into an electromagnet which then rotates the armature. When the armature coils are powered, a magnetic field is created around the armature.
Working
Electric current is supplied to the armature Windings through the brushes. Current flowing through the armature windings produces magnetism in the armature.
This magnetism is react with the magneticism of the field ( either due to permanent magnets or current flow through field coil) and there by force rotation of the armature. As the armature turns, the commutator bans moves from under the brush.
Now the brush will contact the following commulator bar. This start a new turning sequence to keep the motor rotating. As each wdg completes its share of the tunning effort.
It is replaced by a new set of wdg which are located to most effectively use the magnetic field to produce rotation. Automative starters have four field coil and four brushes.
The polarity of the pole pieces alternates first north then south then a north and a south pole. The conductors in both armature and fields are copper bars.
These have minimum resistance and thus permit large current flow. Starting turning effort is directly proportional to the current flow.
When the starter switch is pressed, the motor shaft pinion moves and get locked with the ring gear on the engine flywheel. In this locked position, motor armature shaft cannot rotate it will draw more current and provide maximum torque.
Under this condition, the starter resistance low and due to large torque, motor shaft will start rotating the engine crankshaft.
As the engine crankshaft start rotating, the mechanical load on the armature get reduced and speed increases. This causes increase counter magnetic force.
Once the engine started, the load on the starter completely removed and the starter achieve maximum speed called free speed. During this period, counter electromotive force will be highest and current drawn will be lowest.
Application of Starter Motor
A starter motor is a crucial component in the starting system of an internal combustion engine. Its primary function is to crank the engine and initiate the combustion process, allowing the engine to run on its own.
Main applications and functions of a starter motor:
Starting Internal Combustion Engines:
Automobiles: In most vehicles, the starter motor is used to crank the internal combustion engine. When the driver turns the ignition key, electrical energy from the battery is sent to the starter motor, which then engages the engine’s flywheel and turns it, starting the engine.
Motorcycles: Similar to automobiles, motorcycles also use starter motors to initiate the engine’s operation. In some cases, especially for smaller motorcycles, kick-start mechanisms may be used in conjunction with or instead of electric starter motors.
Marine Engines: Boats and ships with internal combustion engines also utilize starter motors to start their engines.
Generators: Internal combustion engines used in power generators often have starter motors to kick-start the generator when needed.
Construction and Design:
Starter motors are designed to provide a high level of torque for a short duration, as their primary function is to overcome the initial resistance and inertia of the engine to set it in motion.
They typically use a powerful electric motor connected to a gear mechanism (pinion gear) that engages with the engine’s flywheel.
Components and Operation:
Electric Motor: Starter motors are typically electric motors powered by the vehicle’s battery. The electric motor transforms electrical energy into mechanical energy to crank the engine.
Solenoid: A solenoid is often used to engage the starter motor’s gear with the flywheel. It serves as a relay switch that directs electrical current to the starter motor.
Bendix Drive: The bendix drive is a gear and clutch mechanism that engages and disengages the starter motor from the engine’s flywheel. It prevents the starter motor from continuing to turn once the engine is running.
Safety Features:
Modern starter motors are equipped with safety features such as circuitry to prevent engagement while the engine is already running.
They may also have thermal protection to prevent overheating during prolonged cranking.
Maintenance and Troubleshooting:
Starter motors may need periodic maintenance, including checking electrical connections and ensuring proper lubrication of moving parts.
Problems with the starter motor can manifest as difficulty starting the engine, unusual noises, or complete failure to crank the engine.
The starter motor plays a critical role in initiating the operation of internal combustion engines in various applications, ensuring the smooth and reliable starting of vehicles and other machinery.
Troubleshooting of Starter Motor
Troubleshooting a starter motor involves identifying and addressing potential issues that may prevent the engine from cranking properly. Here are some steps you can take to troubleshoot a starter motor:
Check the Battery:
Ensure the battery is fully charged. Low battery voltage can prevent the starter motor from functioning correctly.
Clean and tighten the battery terminals to ensure a good connection.
Inspect the Starter Solenoid:
The solenoid is responsible for engaging the starter motor with the flywheel. Check for any loose or corroded connections.
Listen for a click sound when you turn the ignition key to the start position. If you hear a click but the engine doesn’t crank, it could indicate a faulty solenoid.
Test the Ignition Switch:
Make sure the ignition switch is providing power to the starter when the key is turned to the start position.
Check for any loose or damaged wires connected to the ignition switch.
Look for Loose or Corroded Connections:
Inspect all electrical connections to the starter motor, solenoid, and battery for corrosion or looseness.
Clean and tighten any loose connections.
Check the Starter Motor Connections:
Examine the connections on the starter motor itself. Make sure the wiring is secure and free from damage.
Perform a Voltage Drop Test:
Use a multimeter to check for voltage drops across the starter circuit. Excessive voltage drops can indicate a problem in the wiring.
Measure voltage at the battery, solenoid, and starter motor while attempting to start the engine.
Check for Mechanical Issues:
If the starter motor spins but doesn’t engage with the flywheel, it may have a faulty drive gear or bendix. Inspect for any visible damage.
Ensure the flywheel is not damaged or missing teeth.
Listen for Unusual Noises:
Unusual grinding or whining noises when attempting to start the engine can indicate a problem with the starter motor or its components.
Perform a Bench Test:
If possible, remove the starter motor and perform a bench test. Apply power directly to the motor and observe its performance.
Consider Professional Assistance:
If you’ve checked all the above and cannot identify the issue, or if you lack the necessary tools and experience, consider seeking help from a professional mechanic.
FAQ
What is the purpose of the starter?
A motor starter provides defense by first controlling the electrical output of your device or equipment at its initial point of operation (when you turn it on or activate it).
What happens when the starter motor fails?
Something sounds off. One of the symptoms of a bad starter is a clicking noise when you turn the key or press the start button.
What causes starters to fail?
Faulty electrical connections. Solenoid switch (coupling relay) stiff or faulty. Electrically damaged electric motor. Damaged single pinion gear, starter pinion or freewheel.
How do I know if my starter needs to be replaced?
Loud clicking noise. A single loud click or a series of clicks that occur when you turn the key is a strong indicator of starter motor problems.
Buzzing noise.
Buzzing sounds.
grinding noises.
You may also like