Table of Contents
Hydraulic Actuator
In oil hydraulic system, the oil is allowed to flow through varies elements and actuators (Hydraulic actuator) is the last element in which oil enters and leaves from it to drain to the reservoir for recirculation.
“ The actuators is the component which utilises the oil energy to produce output motion which may be linear or rotary.”
The movement of actuator (linear/rotary) is used for performing the required application.
Below fig. shows the linear actuator which produces push force using oil and it is used for clamping of workpiece on the machine table.

Actuators are the devices which converts fluid power into mechanical power.
The actuator is a hydraulic element which converts oil energy in to mechanical energy for performing the given application.
What is Hydraulic Actuator – Type of Hydraulic Actuator
Need of the Hydraulic Actuators
a) To produce push or pull force

The fluid pushes against the face of the piston and produces push force. The force produced is given by the formula –
F = P . A
Where F = Force in Newton
P = Pressure of oil (n/m2)
A = Area of piston (m2)
When pressurised fluid enters from the rod side of piston, it produces pull force. The force produced is given by the formula –
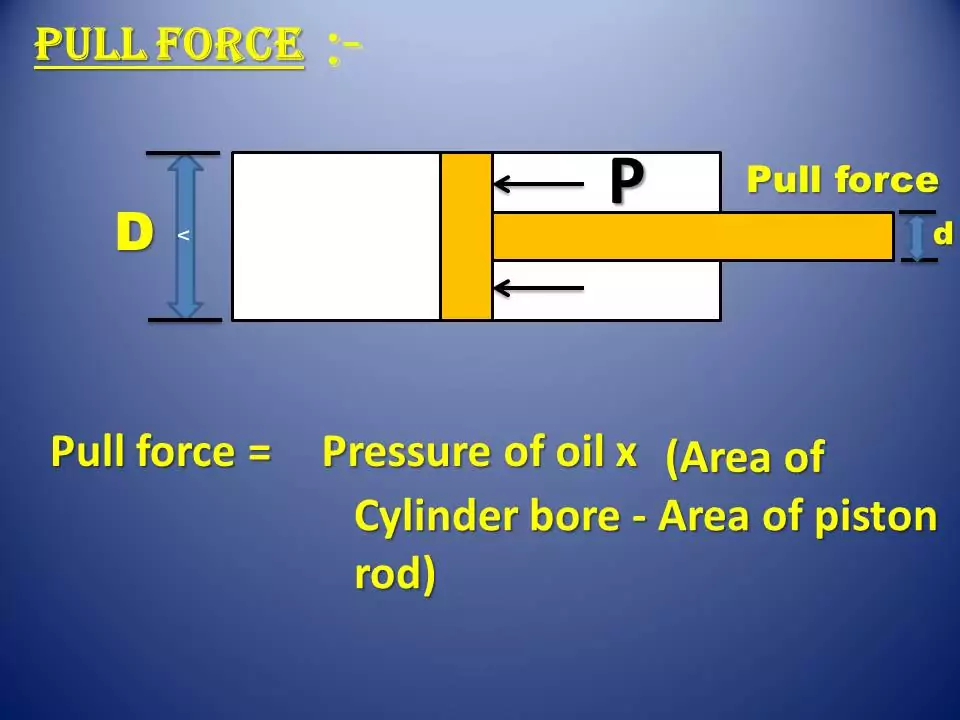
F = P . (A-a)
Where a = Area of piston rod (m2)
Both Push/Pull force can be used for various application like clamping, lifting, material handling, etc.
b) To produce rotary motion
We can utilize oil energy to produce rotary motion.
Which is useful for feed movement of machine table, winding/rewinding etc.
Type of Hydraulic Actuator
a) According to motion
1) Linear actuators – This type of actuator produce linear motion ( to and fro motion) . It is known as hydraulic cylinder.
2) Rotary actuators – This type of actuator produce rotary motion ( angular motion ). It is known as hydraulic motor.
Linear actuators is classified on the basis of –
b) According to oil feed direction
1) Single acting cylinder – When oil is feed only from the face side of the piston. It is called as single acting cylinder. It is also two type
a) Spring return single acting cylinder – When return movement of the actuator is performed by using spring force, it is called as spring return single acting cylinder.
b) Gravity load return Single acting cylinder – When single acting cylinder are mounted vertically, the return movement is carried out through the force of gravity.
2) Double acting cylinder – When cylinders are operated by feeding the oil to the cylinder in both directions i.e. face and rod side it is known as double acting cylinder.
They are further classified as –
a) Double rod type – When piston rod is extended through piston on both side of the piston, it is called as double rod type double acting cylinder.
b) Tandem type – When two cylinders are mounted in line with common piston rod, it is called as tandom double acting cylinder.
c) Ram type – When piston and piston rod of almost same size, the cylinder is known as ram cylinder.
d) Telescopic cylinder – When number of cylinders are mounted in a short retracted envelope like a telescope lenses, it is known as telescopic cylinder.
Rotary actuators
Rotary actuators are classified as
a) As per direction of rotation
1) Uni-directional motors – When oil enters and rotate the motor in either direction ( clockwise or anticlockwise ) it is known as uni-directional motor.
2) Bi-directional motors – When oil is feed alternately from inlets of motor to produce clockwise and counterwise motion, it is known as bi-directional motor.
b) As per construction
1) Gear motors – When gear pair is used, it is known as gear motor.
2) Vane motors – When sliding vanes are used, it is known as vane motor.
3) Piston motors – When piston and cylinder are used, it is known as piston motor.
Piston motors are further classified
a) Axial piston
b) Radial piston
Other criterions for classification of actuators
a) According to construction style
1) Tio rod cylinders – It consists of tie rods which are capable of taking impact load.
2) Mill type cylinders – Steel mills and metal processing industries require its extra ruggedness.
3) Threaded head cylinders – The ends are screwed to the tube by threading outside or inside.
b) According to special application
1) Plunger/ram cylinders
2) Cable cylinders
3) Dulpex cylinders
4) Diaphragm cylinders etc.
Advantages and disadvantages Hydraulic Actuator
Hydraulic actuators are devices that convert hydraulic (fluid) energy into mechanical motion. Here are some of the key advantages and disadvantages of hydraulic actuators:
Advantages:
High Force Output: Hydraulic actuators can generate a significant amount of force or torque, making them suitable for heavy-duty applications such as construction equipment, industrial machinery, and aerospace systems.
Precise Control: They provide precise control over position, velocity, and force due to the inherent characteristics of hydraulic systems. This makes them suitable for applications that require fine-tuned motion control.
Smooth Operation: Hydraulic actuators offer smooth and uniform motion without the jerky starts and stops often associated with some other types of actuators, like pneumatic actuators.
Overload Protection: Hydraulic systems can provide overload protection by limiting the force or pressure applied when a load exceeds a certain threshold. This helps prevent damage to equipment and ensures safety.
Durability: In harsh environments, hydraulic actuators demonstrate their durability and reliability by withstanding contaminants, extreme temperatures, and high loads.
Disadvantages:
Complexity: Hydraulic systems can be complex to design, install, and maintain. They require a network of hoses, valves, pumps, and reservoirs, which can make them more challenging and costly to set up and repair compared to some other actuation methods.
Fluid Leaks: Hydraulic systems are susceptible to fluid leaks, which can be problematic, especially in sensitive environments. Fluid leakage can lead to environmental concerns and a need for constant monitoring and maintenance.
Maintenance: Regular maintenance is essential to keep hydraulic systems operating efficiently. This includes checking fluid levels, replacing seals, and ensuring that all components are in good working condition.
Noise and Vibration: Hydraulic systems can be noisy due to the operation of pumps and the flow of hydraulic fluid. Vibration can also be an issue in some applications, which may require additional measures for noise and vibration control.
Inefficiency: Hydraulic systems can be less energy-efficient compared to some other actuation methods, as they often require a constant supply of hydraulic fluid and may have energy losses due to friction and heat generation.
Environmental Impact: The use of hydraulic fluids can have environmental impacts if not properly managed. Spills or improper disposal of hydraulic fluids can harm the environment and require compliance with regulations.
Hydraulic actuators offer significant advantages in terms of high force output, precise control, and durability, but they also come with disadvantages such as complexity, maintenance requirements, and environmental concerns. The choice to use hydraulic actuators should consider the specific needs of the application and the trade-offs involved.
FAQ
- What are the applications of hydraulic actuators?
Many applications utilize hydraulic actuators now, including winches and crane drives, wheel motors for military vehicles, self-driven cranes, and excavators. - What is meant by hydraulic actuators?
A hydraulic actuator consists of a cylinder or fluid motor that uses hydraulic power to facilitate mechanical operation. The mechanical motion gives an output in terms of linear, rotary or oscillatory motion. - What are the components of hydraulic actuator ?
- It consists of cylinder, piston, spring, hydraulic supply inlet and outlet.
You may also like