Centrifugal pumps, Check out these 60 interview questions and answers covering everything from centrifugal pumps performance curves to maintenance tasks. Learn about the different types of centrifugal pump, their components, and the importance of proper pump selection and maintenance.
What is a centrifugal pump?
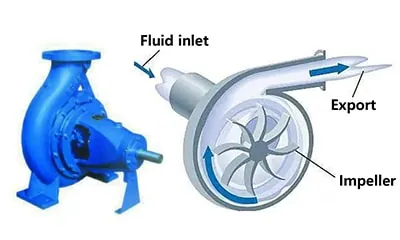
A centrifugal pump is a mechanical device that uses rotational energy to move fluid. It converts rotational kinetic energy into hydrodynamic energy to move liquid.
How does a centrifugal pump work?
A centrifugal pump works by converting rotational energy from an electric motor or engine into hydrodynamic energy. This energy moves liquid through the pump and into the piping system.
What are the different types of centrifugal pumps?
The different types of centrifugal pumps are end suction pumps, split-case pumps, vertical turbine pumps, submersible pumps, and multistage pumps.
What is the maximum efficiency of a centrifugal pump?
The maximum efficiency of a centrifugal pump is around 90%.
What is the minimum flow rate that a centrifugal pump can handle?
The minimum flow rate that a centrifugal pump can handle is usually 10% of its maximum flow rate.
What is the maximum flow rate that a centrifugal pump can handle?
The maximum flow rate that a centrifugal pump can handle depends on its design, but it can range from a few gallons per minute to thousands of gallons per minute.
What is the head of a centrifugal pump?
The head of a centrifugal pump is the height to which the pump can raise a fluid. It is usually measured in feet or meters.
What is the shut-off head of a centrifugal pump?
The shut-off head of a centrifugal pump is the maximum head that the pump can achieve at zero flow.
What is the NPSH of a centrifugal pump?
The NPSH (Net Positive Suction Head) of a centrifugal pump is the pressure required at the suction inlet of the pump to prevent cavitation.
What is cavitation in a centrifugal pump?
Cavitation in a centrifugal pump is the formation of vapor bubbles in the liquid due to a low pressure zone. It can cause damage to the pump impeller and decrease the pump’s efficiency.
How can you prevent cavitation in a centrifugal pump?
Cavitation in a centrifugal pump can be prevented by increasing the NPSH, decreasing the fluid temperature, increasing the pump’s speed, or by using a pump with a larger impeller diameter.
What is the affinity law for centrifugal pumps?
The affinity law for centrifugal pumps states that the flow rate, head, and power consumption of a centrifugal pump are proportional to the speed of the pump.
What is the specific speed of a centrifugal pump?
The specific speed of a centrifugal pump is a dimensionless number that represents the pump’s flow rate, head, and speed. It is used to determine the type of pump needed for a specific application.
What is the difference between a single-stage and a multistage centrifugal pump?
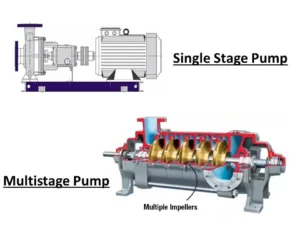
A single-stage centrifugal pump has only one impeller and is used for low-pressure applications. A multistage centrifugal pump has multiple impellers and is used for high-pressure applications.
What is a self-priming centrifugal pump?
A self-priming centrifugal pump is a pump that can automatically prime itself without the need for external priming.
What is the purpose of a volute in a centrifugal pump?
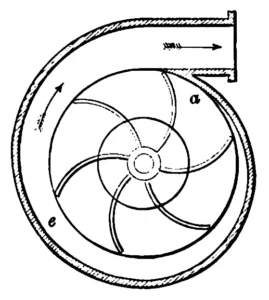
The purpose of a volute in a centrifugal pump is to convert the kinetic energy of the fluid leaving the impeller into pressure energy.
What is the purpose of an impeller in a centrifugal pump?

The purpose of an impeller in a centrifugal pump is to transfer energy from the motor to the fluid.
What is the purpose of a diffuser in a centrifugal pump?
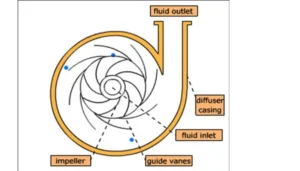
The purpose of a diffuser in a centrifugal pump is to slow down the fluid exiting the impeller and convert its kinetic energy into pressure energy.
What is the purpose of a seal in a centrifugal pump?
The purpose of a seal in a centrifugal pump is to prevent leakage of the fluid from the pump’s casing and to protect the pump’s bearings from the fluid.
What is the difference between a mechanical seal and a packing seal in a centrifugal pump?
A mechanical seal uses two flat faces to seal the fluid, while a packing seal uses a packing material, such as braided graphite, to seal the fluid.
What is the difference between a closed impeller and an open impeller in a centrifugal pump?
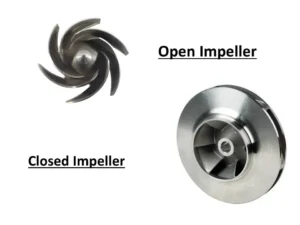
A closed impeller has vanes that are fully enclosed by the impeller shroud, while an open impeller has vanes that are not enclosed by the impeller shroud.
What is the difference between a single volute and a double volute in a centrifugal pump?
A single volute has one curved chamber surrounding the impeller, while a double volute has two symmetrical curved chambers surrounding the impeller.
What is the difference between a single suction and a double suction impeller in a centrifugal pump?
A single suction impeller has a single suction eye, while a double suction impeller has two suction eyes on opposite sides of the impeller.
What is the difference between a horizontal and a vertical centrifugal pump?
A horizontal centrifugal pump has a horizontal shaft, while a vertical centrifugal pump has a vertical shaft.
What is the difference between a centrifugal pump and a positive displacement pump?
A centrifugal pump moves fluid using kinetic energy, while a positive displacement pump moves fluid by trapping a fixed amount of fluid in a chamber and forcing it through the pump’s outlet.
What are the advantages of a centrifugal pump over a positive displacement pump?
Centrifugal pumps are typically more efficient, have lower maintenance requirements, and are better suited for high-flow, low-pressure applications.
What are the disadvantages of a centrifugal pump compared to a positive displacement pump?
Centrifugal pumps are not suitable for high-viscosity fluids and cannot provide a constant flow rate.
What are the different materials used to manufacture centrifugal pumps?
The different materials used to manufacture centrifugal pumps include cast iron, bronze, stainless steel, and plastic.
What are the factors to consider when selecting a centrifugal pump for a specific application?
The factors to consider when selecting a centrifugal pump include the flow rate, head, fluid properties, temperature, and system pressure.
What is the importance of proper pump installation and alignment?
Proper pump installation and alignment are crucial for ensuring the pump’s efficiency, reducing vibration, and prolonging the pump’s lifespan.
What is the importance of regular pump maintenance?
Regular pump maintenance is important for ensuring the pump’s optimal performance, reducing the risk of breakdowns, and prolonging the pump’s lifespan.
What is the importance of pump performance testing?
Pump performance testing is important for verifying the pump’s flow rate, head, and efficiency, and for diagnosing any performance issues.
What are some common causes of pump failure?
Common causes of pump failure include cavitation, excessive vibration, impeller damage, seal failure, and motor failure.
What is the importance of pump efficiency?
Pump efficiency is important for reducing energy consumption, operating costs, and environmental impact.
What are the different methods for controlling pump flow rate?
The different methods for controlling pump flow rate include throttling the discharge valve, adjusting the pump speed, using variable frequency drives (VFDs), and using multiple pumps in parallel or series.
What is the purpose of a suction strainer in a centrifugal pump?
The purpose of a suction strainer in a centrifugal pump is to prevent large solids from entering the pump’s impeller and causing damage.
What is the purpose of a foot valve in a centrifugal pump?
The purpose of a foot valve in a centrifugal pump is to prevent the pump’s casing from becoming empty during operation, which can cause the pump to lose prime.
What is the difference between a self-priming pump and a non-self-priming pump?
A self-priming pump can lift fluid from a lower level to the pump’s suction port without the need for external priming, while a non-self-priming pump requires external priming before it can operate.
What is the difference between a centrifugal pump and a turbine pump?
A centrifugal pump uses centrifugal force to move fluid, while a turbine pump uses the force of a rotating impeller to move fluid.
What is the purpose of a volute casing in a centrifugal pump?
The purpose of a volute casing in a centrifugal pump is to convert the kinetic energy of the fluid leaving the impeller into pressure energy.
What is the purpose of a diffuser casing in a centrifugal pump?
The purpose of a diffuser casing in a centrifugal pump is to further convert the kinetic energy of the fluid leaving the impeller into pressure energy.
What is the NPSH (Net Positive Suction Head) requirement of a centrifugal pump?
The NPSH requirement of a centrifugal pump is the minimum pressure required at the pump’s suction port to prevent cavitation from occurring in the pump’s impeller.
What is cavitation in a centrifugal pump?
Cavitation in a centrifugal pump occurs when the pressure at the pump’s suction port drops below the vapor pressure of the fluid, causing bubbles to form and implode in the pump’s impeller, which can cause damage.
What is the purpose of a hydraulic balance line in a centrifugal pump?
The purpose of a hydraulic balance line in a centrifugal pump is to balance the pressure on both sides of the impeller, which reduces the axial thrust on the pump’s bearings.
What is the purpose of a wear ring in a centrifugal pump?
The purpose of a wear ring in a centrifugal pump is to reduce the clearance between the impeller and the casing, which improves the pump’s efficiency and prolongs the pump’s lifespan.
What is the purpose of a guide vane in a centrifugal pump?
The purpose of a guide vane in a centrifugal pump is to direct the flow of fluid entering the impeller, which improves the pump’s efficiency.
What is the purpose of a coupling in a centrifugal pump?
The purpose of a coupling in a centrifugal pump is to connect the pump’s shaft to the motor’s shaft, which enables the motor to drive the pump.
What is the difference between a close-coupled pump and a frame-mounted pump?
A close-coupled pump has the motor mounted directly on the pump’s casing, while a frame-mounted pump has the motor mounted on a separate baseplate and connected to the pump by a coupling.
What is the difference between a single-stage and a multistage centrifugal pump?
A single-stage centrifugal pump has only one impeller, while a multistage centrifugal pump has two or more impellers connected in series.
What is the purpose of a gland packing in a centrifugal pump?
The purpose of a gland packing in a centrifugal pump is to prevent leakage of fluid along the pump shaft by creating a seal between the shaft and the pump casing.
What is the purpose of a mechanical seal in a centrifugal pump?
The purpose of a mechanical seal in a centrifugal pump is to prevent leakage of fluid along the pump shaft by creating a seal between the shaft and the pump casing using mechanical components.
What are the advantages of a mechanical seal over gland packing?
The advantages of a mechanical seal over gland packing include lower leakage rates, longer lifespan, and reduced maintenance requirements.
What is the purpose of a seal flush in a centrifugal pump?
The purpose of a seal flush in a centrifugal pump is to supply a clean fluid to the mechanical seal, which helps to lubricate and cool the seal and prevent contamination.
What is the purpose of a seal support system in a centrifugal pump?
The purpose of a seal support system in a centrifugal pump is to provide the necessary flow, pressure, and temperature control for the seal flush and cooling water supply.
What is the purpose of a pump performance curve?
The purpose of a pump performance curve is to graphically represent the relationship between the pump flow rate, head, power, and efficiency at different operating conditions.
What is the best efficiency point (BEP) of a centrifugal pump?
The best efficiency point (BEP) of a centrifugal pump is the flow rate at which the pump operates at its highest efficiency.
What is the importance of selecting the correct pump size for an application?
Selecting the correct pump size for an application is important because an oversized pump can result in higher operating costs and decreased efficiency, while an undersized pump can result in reduced performance and premature failure.
What are the different materials used for pump construction?
The different materials used for pump construction include cast iron, stainless steel, bronze, and plastic.
What is the importance of pump maintenance?
Pump maintenance is important to ensure the pump operates at peak efficiency and to prevent premature failure, which can result in downtime and increased operating costs.
What are some common maintenance tasks for centrifugal pumps?
Some common maintenance tasks for centrifugal pumps include checking and adjusting pump alignment, monitoring and maintaining proper lubrication, checking and replacing worn parts, and inspecting and cleaning the pump internals.
How do you calculate NPSHA?
NPSHA is Net positive suction available
NPSHA = Atmospheric pressure + static head – vapor pressure – pressure loss in
the suction piping – pressure loss due to the suction strainer
How to calculate liters per minute (LPM) of pump when four cylinder used on power pack?
The liters per minute (LPM) of a pump in a power pack with four cylinders can be calculated using the following steps:
Determine the displacement of one cylinder in the power pack. This information can be found in the manufacturer’s specifications or by measuring the piston bore and stroke of one cylinder. Let’s assume the displacement of one cylinder is 50 cc.
Calculate the total displacement of all four cylinders by multiplying the displacement of one cylinder by the number of cylinders. In this case, the total displacement would be 50 cc x 4 = 200 cc.
Determine the pump’s efficiency factor. This is typically provided by the manufacturer and represents the percentage of the theoretical flow that the pump can actually deliver. Let’s assume the efficiency factor is 90%.
Calculate the theoretical flow rate of the pump by multiplying the total displacement of the cylinders by the pump’s rotational speed in revolutions per minute (RPM) and dividing by 1,000. For example, if the pump’s RPM is 1,000, the theoretical flow rate would be:
Theoretical Flow Rate = (Total Displacement x RPM) / 1,000
Theoretical Flow Rate = (200 cc x 1,000 RPM) / 1,000
Flow Rate (Theoretical) = 200 LPM
Calculate the actual flow rate of the pump by multiplying the theoretical flow rate by the pump’s efficiency factor. For example, if the efficiency factor is 90%, the actual flow rate would be:
Actual Flow Rate = Theoretical Flow Rate x Efficiency Factor
Actual Flow Rate = 200 LPM x 0.9
Flow Rate (Actual) = 180 LPM
Therefore, the LPM of the pump with four cylinders in this example is 180 LPM.
You may also like