Table of Contents
Definition
Gas Charged Accumulator store energy with the help of compressed gas.
A gas charged accumulator is a type of hydraulic accumulator that stores energy in the form of compressed gas or nitrogen. It consists of a pressure vessel or cylinder with a movable piston, bladder, or diaphragm that separates the gas chamber from the hydraulic fluid chamber.
Here’s how a gas charged accumulator typically operates
Gas charge: The gas chamber of the accumulator is pre-charged with compressed gas, usually nitrogen. This gas charge provides the energy storage capacity of the accumulator.
Hydraulic fluid entry: When the hydraulic system is active, hydraulic fluid enters the accumulator through an inlet valve. The gas chamber is separated from the hydraulic fluid chamber by the piston, bladder, or diaphragm.
Compression: As the hydraulic fluid enters the accumulator, it compresses the gas in the gas chamber. The gas gets compressed, storing potential energy in the form of high-pressure gas.
Energy storage: The compressed gas serves as a source of stored energy. This energy can be released later when there is a demand for additional hydraulic power.
Energy release: When the hydraulic system requires additional power, the pressurized hydraulic fluid is released from the accumulator through an outlet valve, and the gas expands to provide the necessary force. This release of energy can occur rapidly, delivering a surge of pressurized fluid to meet the system’s demand.
Gas charged accumulators offer several advantages, including
Rapid response: Gas charged accumulators provide quick response times due to the compressibility of the gas. They can deliver high-pressure fluid rapidly, making them suitable for applications that require immediate and precise power assistance.
Energy storage capacity: Gas charged accumulators have a high energy storage capacity, allowing them to store large volumes of energy for later use. This stored energy can be released quickly when needed, providing supplemental power during peak demands or emergencies.
Pressure stabilization: Gas charged accumulators help stabilize pressure fluctuations in hydraulic systems, absorbing shocks and variations caused by changes in demand or pump fluctuations. This helps maintain system performance and stability.
Improved efficiency: By utilizing the stored energy during peak demands, gas charged accumulators can help reduce the load on the hydraulic pump and increase overall system efficiency. This can lead to energy savings and potentially smaller pump size requirements.
Construction
It consists of a precharged gas chamber and a fluid chamber. The fluid chamber is connected to a hydraulic system. The chambers are separated by a bladder, a piston, or any kind of a diaphragm.
It consists of a synthetic polymer rubber bladder fitted inside a metal shell. The bladder is fitted with compressed gas.
A poppet valve is located at the discharge port get closed when accumulator is completely charged.
The accumulator is precharged when it is empty (oil is not present) with the help of of gas charging inlet.
Generally dry nitrogen gas is used to to fill the bladder.

Working
Initially the accumulator is precharged to the required pressure with the compressed gas in the bladder.
When oil under pressure enters in the accumulator through inlet, it starts pushing the bladder with the oil pressure.
As the gas inside the bladder is compressible, the oil push the bladder in the upward direction and compress the bladder when oil pressure is more than force of the bladder.
The accumulator is completely charged when bladder is compressed sufficiently. Gas expands during unloading the accumulator to the required application device.
Symbol
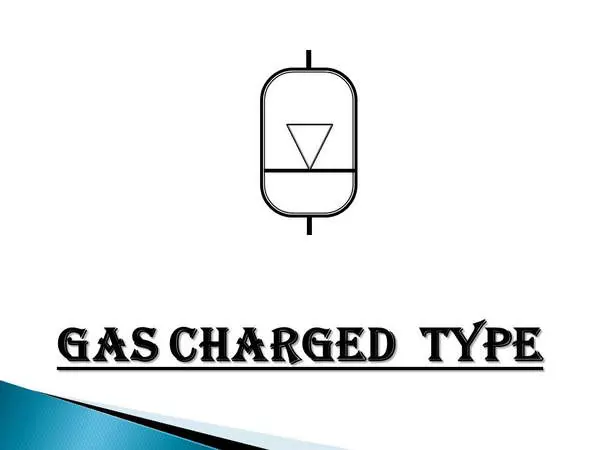
Advantages
The accumulator is compact in design.
Quick response for loading or unloading time.
High energy storage capacity: Gas charged accumulators have a higher energy storage capacity compared to some other types of accumulators. The compressibility of the gas allows for the storage of a larger volume of energy within the accumulator, which can be quickly released when needed.
Rapid response time: Gas charged accumulators provide rapid response times due to the compressibility of the gas. When there is a sudden demand for hydraulic power, the gas can quickly expand, delivering a surge of pressurized fluid to meet the demand. This makes them suitable for applications that require quick and precise responses, such as hydraulic shock absorption or emergency power assistance.
Reduced pressure fluctuations: Gas charged accumulators help to reduce pressure fluctuations in hydraulic systems. They act as a pressure reservoir, absorbing pressure variations caused by changes in demand or pump fluctuations. This leads to smoother and more consistent operation of the hydraulic system, enhancing overall performance.
Long service life: Gas charged accumulators tend to have a longer service life compared to some other types of accumulators. The separation of the gas and hydraulic fluid helps to protect the internal components from wear and corrosion, resulting in extended durability and reliability.
Disadvantages
Constant pressure can not be maintained due to compressible nature of gas.
Higher pressure ratio and higher temperature may cause failure of bladder.
Limited temperature range: Gas charged accumulators have a limited temperature range within which they can operate effectively. Extreme temperatures can affect the performance and reliability of the gas charge, potentially leading to reduced functionality or failure of the accumulator.
Maintenance requirements: Gas charged accumulators require regular inspection and maintenance to ensure proper functioning. The gas charge pressure needs to be monitored and adjusted periodically to maintain optimal performance. Additionally, the seals and bladder (if used) should be inspected for leaks or damage.
Initial cost: Gas charged accumulators tend to have higher initial costs compared to some other types of accumulators. The design complexity and the need for specialized components can contribute to a higher price point. However, the long service life and performance benefits may justify the initial investment in certain applications.
Gas leakage concerns: There is a possibility of gas leakage over time, which can affect the performance of the accumulator. Regular checks for gas leaks and proper maintenance are necessary to ensure the integrity of the gas charge.
Application of Gas Charged Accumulator
Gas charged accumulators find application in various industries and systems where they can provide specific benefits. Some common applications of gas charged accumulators include:
Hydraulic systems: Gas charged accumulators are widely used in hydraulic systems to store energy and provide supplemental hydraulic power when needed. They can assist in absorbing shocks and vibrations, dampening pressure fluctuations, and delivering quick bursts of high-pressure fluid for various tasks. Hydraulic presses, cranes, elevators, and heavy machinery often utilize gas charged accumulators.
Energy storage systems: Gas charged accumulators can be employed in energy storage systems, particularly in renewable energy applications. They can store excess energy generated from renewable sources like wind turbines or solar panels during periods of low demand and release it during peak demand or when the primary power source is unavailable. This allows for a more stable and reliable energy supply.
Suspension systems: Gas charged accumulators are commonly used in vehicle suspension systems, such as in automobiles, motorcycles, and off-road vehicles. They help absorb shocks and provide a smoother ride by controlling the compression and rebound of the suspension. Gas charged accumulators offer adjustable suspension settings and can adapt to changing road conditions.
Aerospace and aviation: Gas charged accumulators play a vital role in aerospace and aviation applications. They are utilized in landing gear systems, aircraft brakes, thrust reversers, and other hydraulic systems. Gas charged accumulators provide emergency power for critical operations, shock absorption during landings, and hydraulic energy storage for various aircraft functions.
Industrial machinery and manufacturing: Gas charged accumulators are employed in various industrial machinery and manufacturing processes. They can be used in stamping and pressing machines, injection molding equipment, hydraulic clamps, and robotic systems. Gas charged accumulators assist in delivering rapid and precise hydraulic power for specific operations and help mitigate pressure fluctuations.
FAQ
When should I charge my accumulator?
If the accumulator is to be used to add volume to the system, its pre-charge must be somewhat below the maximum system pressure so oil can enter it.
What pressure should an accumulator be charged to?
Manufacturers specify recommended precharge pressure for their accumulators. In energy-storage applications, a bladder accumulator typically is precharged to 80% of minimum hydraulic system pressure and a piston accumulator to 100 psi below minimum system pressure.
Which gas is used in accumulator?
The accumulators use nitrogen to keep the hydraulic fluid pressurized. When the fluid is pumped into an accumulator the nitrogen (N2) inside the accumulator is compressed.
What are the four functions of an accumulator?
Hydraulic accumulators are able to provide a handful of functions: Energy storage, leakage compensation, and vibration and shock reduction.
How do you check accumulator pre charge pressure?
The hydraulic gauge will slowly drop as oil is discharged. Once all the oil is out of the accumulator, the pressure gauge will rapidly drop to 0 PSI. The pressure where the needle rapidly drops is the pre-charge pressure.
You may also like